
图①:旅大5-2北油田作业平台局部。
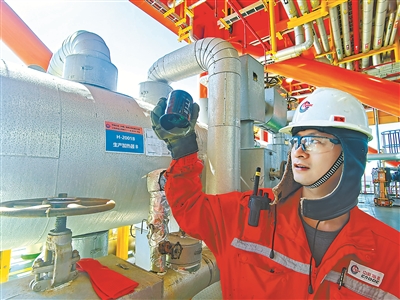
图②:工作人员在展示超稠油的黏度。
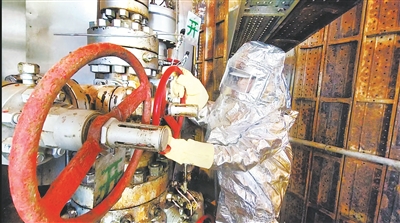
图③:工作人员身着隔热服在进行注热井口流程倒运作业。
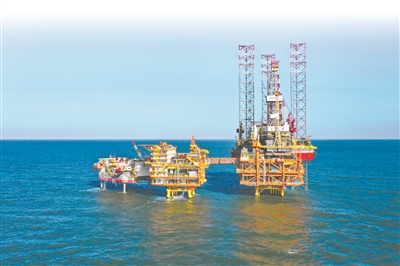
能源,人类社会发展的重要基础资源。
渤海东北部,辽东湾海域。世界首个海上超稠油储量规模化开发油田——旅大5-2北油田的生产平台傲然挺立于此。
9吨、60吨、109吨……投产近一个月,该油田首口超稠油蒸汽吞吐井日产油量逐步攀升,基本达到开发方案设计高峰产量。该模式的成功应用,将撬动渤海湾盆地上亿吨宛如“黑琥珀”一般的特超稠油资源开发,对于保障国家能源安全意义重大。
什么是稠油、超稠油?我国稠油开发现状如何?令人“愁上加愁”的超稠油开发到底难在哪儿?全球首个海上大规模超稠油热采开发油田投产背后有何技术突破?记者近日采访了中国海洋石油集团有限公司有关负责同志。
唤醒沉睡的“海底黄金”
变规模储量为产量
润滑油、润滑脂,交通建筑行业所用的各类型沥青,工业及发电厂用燃料油……未来,市面销售使用的这些产品中,或许有不少将源自渤海湾盆地的超稠油。
据中国海油有关负责人介绍,4月23日一期投产的旅大5-2北油田项目,完全投产后预计可累产原油超650万吨,全部炼化成沥青可铺设5000余公里的4车道高速公路,相当于北京到三亚的直线往返距离。与我国其他海上油田不同,旅大5-2北油田属于非常规稠油,地层原油黏度大多超过50000毫帕秒,是渤海已开发最稠原油的20倍以上。
这是一个什么概念?“常温下接近固体沥青,根本无法流动。”中国海油天津分公司渤海石油研究院油藏总师刘英宪给记者举了两个例子,“我们平时吃的蜂蜜黏度通常是3000毫帕秒左右,而使用的面霜黏度通常在10000毫帕秒左右。”
记者了解到,开采后未经任何加工的石油,被称作原油,是一种复杂的混合物,主要包含各种烃类、胶质、沥青质等。不同油田中,受油层埋藏深度、盖层状况及运移距离等因素影响,产出原油的颜色、组分、黏度或密度等都存在差异。
“黏度超过50毫帕秒的原油就属于稠油,被视为‘地下黄金’。”刘英宪解释道,50毫帕秒相当于常温下奶油的黏度。在此基础上,以10000毫帕秒、50000毫帕秒为分界点,又可以将稠油分为普通稠油、特稠油和超稠油。
数据显示,在世界剩余石油资源中,约有70%都是稠油。持续、有效、经济的稠油开发成为各国石油增产的主攻方向。
作为世界四大稠油生产国之一,我国稠油资源量约有198.7亿吨,现已探明35.5亿吨,开发潜力巨大。仅在渤海海域,稠油储量就占了原油总探明储量的近一半。唤醒这部分沉睡的“海底黄金”,变规模储量为产量,对我国能源安全的重要性不言而喻。
然而,稠油开采并不容易。
专家介绍,犹如“黑琥珀”一般的稠油在行业中还有一个名字——“愁油”。因为黏度大、流动性差,其开采难度大、成本高,多年来一直是人类“可望而不可即”的黑色宝藏。尤其是海上油田不能像陆地油田那样布置密集的井网,想要将稠油从海底地层提升到地面再完成输送,对采油技术、流程处理、海管外输等都提出了极高的要求,是公认的世界级开采难题。海上超稠油的开采更是令人“愁上加愁”。
如何有效撬动这些稠油储量,找到适合海上高效开发的“良方”,成为我国科研攻关的重要内容。
从方案设计到机理表征,从效果评价到接替技术……一系列研究与技术攻关,让我国海上稠油开发接连取得重要突破。2010年,绥中36-1油田一期综合调整项目投产,打破了常规稠油水驱开发采收率不超过20%的预言;2020年,我国海上首座大型稠油热采开发平台——旅大21-2平台顺利投产,填补了我国海上油田稠油规模化热采的技术空白。今年4月,旅大5-2北超稠油油田的投产,则标志着我国海上稠油开发进入新的阶段。
给海底油层“蒸桑拿”
精准确定拐点温度让稠油变稀油
稠油虽然顽固,但也有弱点——怕热。
试验数据显示,温度每升高10摄氏度,稠油黏度就会降低一半左右。
因此,与常规原油“冷采”的开发模式不同,稠油通常是采用“热采”模式。即向地层注入热水或高温高压蒸汽,以提高地层中原油的温度,从而降低原油黏度,让其变成流动性很好的“稀油”,然后趁热将这些“稀油”开采出来。
业内专家介绍,目前常用的稠油“热采”模式有两种。一种是“蒸汽驱”模式,就是向井中持续注入高温高压蒸汽,通过蒸汽将地下原油加热,然后“你推我搡”,将邻近变稀的原油驱向采油井采出。另一种则是“蒸汽吞吐”模式,就是先将高温高压的蒸汽注入油层,对油井周围油层加热降黏,焖井换热后再开井采油。旅大5-2北油田采用的是“蒸汽吞吐”模式。
注汽、焖井、开采……刘英宪形象地给记者打了个比方,“这就像是给海底油层‘蒸桑拿’”。
不过,给稠油“蒸桑拿”不是一项简单的工程。
要达到多高的温度才能让稠油变稀、蒸汽注入如何才能更加均匀、变稀的原油怎么才能顺利采出……这都是要攻克的技术难点。
准确确定稠油变稀的拐点温度,是旅大5-2北油田能否顺利开发的关键。“只有确保注热后,地层、井筒和地面管线中原油的温度都高于这个拐点温度,稠油才能被顺利采出。”刘英宪告诉记者,而这也是困扰行业多年的难题。
“并非稠油黏度越大拐点温度越高,即便是黏度相近,不同油田的原油拐点温度也可能相差很大。”有关科研人员介绍,通过大量试验,他们摸索出一套定量计算拐点温度的方法,并发现旅大5-2北油田原油虽然黏度超过50000毫帕秒,但是拐点温度却与已开发油田普通稠油的拐点温度相近。
“很高兴,这说明旅大5-2北油田超稠油走‘蒸汽吞吐’开发这条路可行!”刘英宪说,为了验证计算结果的可靠性,科研人员还精心设计了验证方案,最后通过几百组实验数据,证实了旅大5-2北油田原油的拐点温度约为90℃。
“‘蒸桑拿’用的水十分讲究,要使用经过严格处理的纯净水。”中国海油天津分公司副总工程师刘义刚告诉记者。
然而,对于海上作业平台来说,淡水资源匮乏,只能从海水或地层水中做出选择。专家介绍,海水与地层水各有优劣:海水淡化能提供的水量更大,但处理流程较长且较复杂;地层水处理流程相对简便,但其中若含油,会导致水处理流程中的膜组件失效,无法生产出合格的锅炉供水。如何在降本增效的前提下规避风险?
研究人员反复论证,最终研发出首套海上双水源锅炉水处理系统。该系统以使用地层水为水源作为设计基础,在生产过程中,一旦监测到地层水中含油不再适合作为锅炉供水水源,便可通过简单的设备更换和管线连接切换为海水水源。如此一来,投资成本较传统海水淡化系统可降低约30%。
与此同时,由于蒸汽的波及范围有限,且离注汽井越远,热能就会不断递减。为提高注入蒸汽的热利用率和经济效益,研究人员还创新形成了注蒸汽波及范围定量预测技术,建立了厚层稠油油藏注蒸汽波及范围预测模型,可对不同原油黏度和油层厚度下注入蒸汽垂向波及系数进行评价,根据评价结果动态适时调整参数,控制蒸汽注入速度和注入量。
创新实行注采一体化
注热与生产高效衔接
产油量、含水量、设备压力值……5月12日,记者电话连线中国海油天津分公司渤海石油研究院采油工艺研究所工程师王弘宇时,她正根据旅大5-2北油田作业平台反馈的首口超稠油井作业参数,分析射流泵生产运行情况,为后续热采井投产提供技术支持。
射流泵注采一体化工艺,是从地层经济高效地将原油举升上来的核心工艺,也是稠油热采领域的一项重大创新。
“我们采用的射流泵注采一体化工艺,就是注热过程和生产过程共同使用一套井筒管柱,实现了注热与生产的高效衔接。”刘义刚介绍。
由于海上油田作业平台面积有限、油井轨迹复杂等,不能采用陆地上超稠油生产常用的有杆式抽油机,而常规的注采两趟管柱是注蒸汽时下入注热管柱,开采时提出注热管柱再下入生产管柱,会耗费大量时间和作业成本。科研人员经反复比对论证,创新采用射流泵注采一体化管柱技术,将注热管柱与生产管柱合二为一,极大降低了修井时间,节省修井作业成本达30%以上。据测算,26口井8个轮次作业累计可节约操作费用超过2亿元,大幅提高超稠油热采规模开发的经济性。
“旅大5-2北油田作业平台分为井口平台和生产支持平台,两个平台通过栈桥连接,投影面积加起来还没有一个标准足球场大。而对于热采平台来讲,无论是工序、工艺,还是配套设施,都更为复杂。”刘义刚告诉记者。
以注入程序为例。对于常规冷采平台而言,配套注水设备即可。而热采平台不仅需要增加专门的水处理设备,还需要增加适用于规模化热采的大排量锅炉及相关配套设施。因此在设计伊始,科研人员就将这些因素考虑在内,相关配套设施尽可能小型化、轻量化。据了解,项目创新形成的规模化热采大排量蒸汽锅炉设备,不仅实现4井同注,具备过热功能,而且极大降低了占地面积。同时应用静电聚集分离器+旋流除砂分离器,实现生产阶段超稠油、水、砂的高效分离。
不仅如此,设备的抗高压高温能力、保温效果、注热安全等也是科研人员的重要考量。
一方面科研人员对注热管柱开展深入研究,攻关形成全密闭无热点的高干注汽管柱工艺,极大降低井筒的热损失,保障了注热效果。另一方面创新形成包含高温井下安全阀、高温热采封隔器等关键工具的高温井下安全控制系统,达到国际领先水平,为旅大5-2北油田开发筑牢安全屏障。
高温井下安全控制、射流泵注采一体化、海上小型多功能热采装备、物模数模一体化设计……一系列技术攻关,让我国实现超稠油规模化、经济开发的突破。(本报记者王珍)